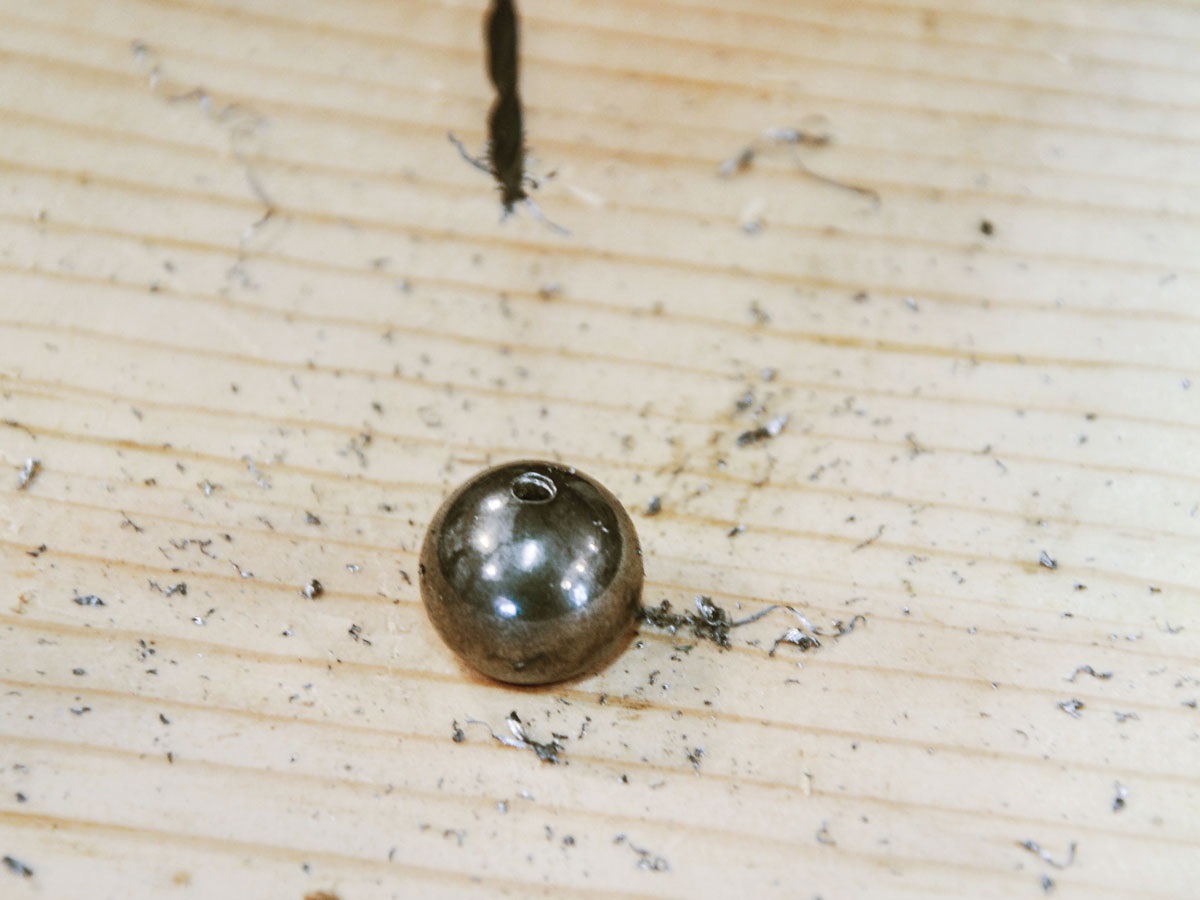
In the pursuit of enhancing automotive engine performance, engineers and enthusiasts alike constantly seek innovative methods to optimize combustion efficiency, increase power output, and improve overall reliability.
Among the various techniques employed, the utilization of drilled balls in engine components has garnered significant attention in recent years. This article delves into the intricacies of drilled balls, their impact on engine performance, and the considerations surrounding their implementation in automotive engines.
Understanding Drilled Balls
Drilled balls, also known as ball drilling, represent a machining process integral to various industrial applications, including automotive engineering.
This section delves into the fundamentals of drilled balls, elucidating their construction, applications, and underlying principles.
What are Drilled Balls?
Drilled balls, or ball drilling, entail a machining process where spherical or cylindrical objects, typically metallic alloys, are punctured with precision-drilled holes. The diameter, depth, and arrangement of these holes vary based on intended applications and desired outcomes.
The Science Behind Drilled Balls
The integration of drilled balls in automotive engines is grounded in fluid dynamics and thermodynamics principles.
By strategically positioning drilled balls within engine components, engineers aim to manipulate airflow, turbulence, and combustion characteristics to optimize performance metrics such as horsepower, torque, and fuel efficiency.
Applications of Drilled Balls in Automotive Engines
Drilled balls play a pivotal role in optimizing automotive engine performance and efficiency by enhancing airflow dynamics, and combustion processes, and reducing friction.
This section explores the diverse applications of drilled balls within automotive engines and their impact on overall engine operation.
Enhancing Airflow Dynamics
A primary application of drilled balls in automotive engines is optimizing airflow dynamics within the intake and exhaust systems.
By placing drilled balls within intake manifolds, engineers induce turbulence, promoting better air-fuel mixing, and leading to improved combustion efficiency and enhanced power output.
Optimizing Combustion
Drilled balls play a crucial role in optimizing combustion processes within engine cylinders.
Integrated into piston designs or cylinder heads, they facilitate uniform distribution of fuel-air mixture, reduce detonation tendencies, and mitigate heat concentration, enhancing both performance and durability.
Minimizing Friction and Wear
Beyond airflow and combustion improvement, drilled balls help minimize friction and wear within the engine’s moving components.
By strategically placing them in high-friction areas such as camshaft bearings or piston skirts, engineers reduce contact surface area, mitigate metal-on-metal wear, and prolong critical engine parts’ lifespan.
Benefits of Using Drilled Balls
The integration of drilled balls into automotive engines offers a myriad of benefits, ranging from improved performance metrics to enhanced reliability. This section outlines the significant advantages associated with employing drilled balls within engine components.
Improved Performance Metrics
Integration of drilled balls into automotive engines enhances performance metrics like horsepower, torque, and throttle response.
By optimizing airflow, combustion, and friction characteristics, drilled balls unlock latent engine potential, resulting in noticeable gains in acceleration and driving dynamics.
Enhanced Fuel Efficiency
Drilled balls contribute to improved fuel efficiency by promoting efficient combustion and reducing parasitic losses due to friction and wear.
Engines equipped with drilled balls achieve higher thermal efficiencies and consume less fuel for a given power output, translating into gains in miles per gallon (MPG) and reduced carbon emissions.
Enhanced Reliability and Durability
Contrary to conventional wisdom, drilled balls enhance engine reliability and durability. By minimizing hot spots, reducing thermal gradients, and mitigating wear on critical components, they prolong engine internals’ lifespan, reducing premature failures and costly repairs.
Challenges and Considerations
While the integration of drilled balls offers numerous benefits for enhancing automotive engine performance, several challenges and considerations must be addressed to ensure successful implementation.
This section highlights key challenges and considerations associated with utilizing drilled balls within automotive engines.
Manufacturing Complexity
Widespread adoption of drilled balls faces challenges due to inherent manufacturing complexity. Precision-drilled balls require advanced machining techniques and quality control measures to ensure reliability and performance consistency.
Integration into Existing Designs
Seamless integration of drilled balls into existing engine designs poses challenges. Retrofitting older engines may require extensive modifications, potentially outweighing performance benefits in terms of cost and feasibility.
Long-Term Reliability and Maintenance
While offering promising benefits, drilled balls’ long-term reliability and maintenance requirements remain under scrutiny.
Factors like debris accumulation, corrosion, and material fatigue could compromise component integrity, necessitating periodic inspection and replacement.
Future Perspectives and Innovations
Continued research and development efforts aimed at refining manufacturing techniques, optimizing design parameters, and addressing reliability concerns will broaden drilled ball technology adoption.
Advancements in materials science, additive manufacturing, and computational fluid dynamics (CFD) will further enhance drilled ball efficacy and applicability, reshaping automotive engineering landscapes.
Conclusion
Drilled balls represent a promising approach to optimizing engine performance and efficiency in automotive applications. Leveraging fluid dynamics, thermodynamics, and precision machining, engineers can enhance airflow dynamics, combustion efficiency, and friction characteristics within automotive engines.
Despite challenges, ongoing research and innovation efforts will unlock drilled ball technology’s full potential, shaping automotive engineering and driving experiences globally.