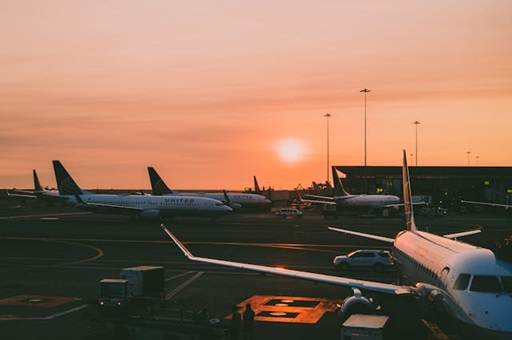
In the aviation industry, the topmost concern is guaranteeing the safe and efficient operation of all aircraft. This means relying on high-quality, dependable airplane parts. These parts are not just essential for optimal performance, but also for safeguarding the lives of passengers and crew. Whether you manage a small airline, a private jet, or a large commercial fleet, informed decision-making when purchasing aircraft parts is critical. Here are four key considerations:
Verify Authenticity and Certification
In the aviation industry, procuring authentic and certified airplane parts is absolutely paramount. Stringent regulations set by organizations like the FAA and EASA govern how these parts are made and tested. Verifying proper documentation and certifications for each part is essential. This process ensures the parts meet the industry’s rigorous safety standards, directly safeguarding lives. To guarantee authenticity, purchasing from reputable suppliers and manufacturers is crucial. Counterfeit parts are a serious threat, potentially causing catastrophic failures.
Authentic parts have a traceable history, detailing their origin, manufacturing process, and any past use. Maintaining this history is vital for ensuring an aircraft’s airworthiness and keeping accurate maintenance records. When verifying the authenticity and certification of airplane parts, ensure that any components requiring hydraulic fluids are compatible with industry-standard fluids like 5606 hydraulic fluid to maintain optimal performance and safety.
Assess Compatibility and Specifications
When it comes to airplane parts, compatibility is king. Every aircraft model boasts unique specifications, and using parts not designed for yours can lead to trouble. Think of it like fitting a square peg in a round hole – it might seem like it works, but inefficiencies or even mechanical failures could arise. To ensure a smooth flight (pun intended!), carefully review the technical specs of the parts you’re considering. Then, double-check them against your aircraft’s maintenance manual and manufacturer guidelines.
This ensures everything is in perfect harmony. Do not hesitate to seek the wisdom of experienced aviation mechanics or engineers. Their expertise can be invaluable in confirming compatibility and helping you avoid costly mistakes. They might also point out potential modifications or adjustments needed to integrate the new parts into your aircraft. Remember, these modifications can add to the overall cost and downtime, so factor them into your decision-making process from the start.
Inspect Quality and Condition
Ensuring the quality and condition of airplane parts is absolutely critical. The safety and performance of an aircraft depend heavily on several crucial factors. Consequently, there can be no shortcuts when it comes to parts. New components must be flawless and of the highest quality. When considering used or overhauled parts, a meticulous inspection is essential to assess their current state and remaining lifespan. If you’re purchasing used parts, obtaining detailed maintenance and service records is crucial.
These records provide a history of the part’s usage, including any repairs, modifications, and its current condition. To further ensure reliability, consider engaging a certified aviation maintenance technician to perform a physical inspection. This inspection should focus on signs of wear and tear, corrosion, and any past damage. For an extra layer of confidence, non-destructive testing (NDT) methods, like X-rays or ultrasounds, can be employed to detect internal flaws invisible to the naked eye. These comprehensive measures will give you peace of mind, knowing your aircraft parts are up to the rigorous demands of flight.
Evaluate Vendor Reputation and Support
When purchasing airplane parts, choosing a reputable vendor is paramount. These vendors prioritize strict quality control, ensuring the parts you receive are genuine and certified to meet aviation safety standards. Thorough research is key. Look for customer reviews, industry certifications, and the vendor’s experience within the aviation market. Do not overlook customer support and after-sales service.
A reliable vendor offers comprehensive assistance, including technical expertise, warranty coverage, and a streamlined process for returns or exchanges should problems occur. Building a strong relationship with your vendor can unlock benefits like better pricing, faster responses to your needs, and access to valuable industry knowledge. Finally, consider parts availability. In aviation, minimizing downtime is critical. Vendors with a substantial inventory and an efficient supply chain can significantly reduce the time it takes to acquire necessary parts, keeping your operations running smoothly.
Conclusion
Ensuring every aircraft component functions flawlessly is vital. Before acquiring parts, prioritize safety and efficiency with four key checks. Verify authenticity and certifications for guaranteed performance. Ensure compatibility and specifications match your exact aircraft model. Inspect quality and condition with a trained professional. Finally, evaluate the vendor’s reputation and support for long-term peace of mind. These steps guarantee airworthiness, optimal performance, and the highest safety standards for all.